Abstracts
Due to the development of nanoscience, the interest in electrochromism has increased and new assemblies of electrochromic materials at nanoscale leading to higher efficiencies and chromatic contrasts, low switching times and the possibility of color tuning have been developed. These advantages are reached due to the extensive surface area found in nanomaterials and the large amount of organic electrochromic molecules that can be easily attached onto inorganic nanoparticles, as TiO2 or SiO2. Moreover, the direct contact between electrolyte and nanomaterials produces high ionic transfer rates, leading to fast charge compensation, which is essential for high performance electrochromic electrodes. Recently, the layer-by-layer technique was presented as an interesting way to produce different architectures by the combination of both electrochromic nanoparticles and polymers. The present paper shows some of the newest insights into nanochromic science.
nanochromics; nanoparticles; layer-by-layer; viologens
Com o desenvolvimento da nanociência, o estudo do fenômeno do eletrocromismo desperta forte e continuado interesse devido à possibilidade de obter maiores eficiências eletrocrômicas, contrastes cromáticos, sintonização de cores e baixos tempos de resposta por meio da montagem de nanomateriais. Estas vantagens são possíveis devido à alta área superficial que os nanomateriais possuem e a enorme quantidade de moléculas orgânicas eletrocrômicas que podem ser facilmente ligadas a nanopartículas inorgânicas como TiO2 ou SiO2. Somado a isto, o contato direto entre o eletrólito e os nanomateriais produz altas velocidades de transferência iônica, com a concomitante compensação de carga rápida, o que é essencial para preparar eletrodos eletrocrômicos de alto desempenho. Recentemente a técnica de deposição eletrostática camada por camada foi apresentada como uma maneira interessante de preparar diferentes arquiteturas combinando nanopartículas e polímeros. O presente trabalho mostra alguns dos últimos avanços em nanocromismo.
REVIEW
Nanochromics: old materials, new structures and architectures for high performance devices
Marcio VidottiI; Susana I. Córdoba de TorresiII,* * e-mail: storresi@iq.usp.br
IInstituto of Chemistry, University of Campinas, UNICAMP, P.O. Box 6154, 13083-970 Campinas-SP, Brazil
IIInstituto de Química, Universidade de São Paulo, CP 26077, 05513-970 São Paulo-SP, Brazil
ABSTRACT
Due to the development of nanoscience, the interest in electrochromism has increased and new assemblies of electrochromic materials at nanoscale leading to higher efficiencies and chromatic contrasts, low switching times and the possibility of color tuning have been developed. These advantages are reached due to the extensive surface area found in nanomaterials and the large amount of organic electrochromic molecules that can be easily attached onto inorganic nanoparticles, as TiO2 or SiO2. Moreover, the direct contact between electrolyte and nanomaterials produces high ionic transfer rates, leading to fast charge compensation, which is essential for high performance electrochromic electrodes. Recently, the layer-by-layer technique was presented as an interesting way to produce different architectures by the combination of both electrochromic nanoparticles and polymers. The present paper shows some of the newest insights into nanochromic science.
Keywords: nanochromics, nanoparticles, layer-by-layer, viologens
RESUMO
Com o desenvolvimento da nanociência, o estudo do fenômeno do eletrocromismo desperta forte e continuado interesse devido à possibilidade de obter maiores eficiências eletrocrômicas, contrastes cromáticos, sintonização de cores e baixos tempos de resposta por meio da montagem de nanomateriais. Estas vantagens são possíveis devido à alta área superficial que os nanomateriais possuem e a enorme quantidade de moléculas orgânicas eletrocrômicas que podem ser facilmente ligadas a nanopartículas inorgânicas como TiO2 ou SiO2. Somado a isto, o contato direto entre o eletrólito e os nanomateriais produz altas velocidades de transferência iônica, com a concomitante compensação de carga rápida, o que é essencial para preparar eletrodos eletrocrômicos de alto desempenho. Recentemente a técnica de deposição eletrostática camada por camada foi apresentada como uma maneira interessante de preparar diferentes arquiteturas combinando nanopartículas e polímeros. O presente trabalho mostra alguns dos últimos avanços em nanocromismo.
Abbreviations
ECM(ox): electrochromic material in oxidized form; ECM(red): electrochromic material in reduced form; CV: cyclic voltammetry; η: electrochromic efficiency, defined by the relation between change in absorbance and the electric charge spent in the process; ΔA: change in absorbance; ΔT %: change in transmittance or contrast; τ: response time, the time required for a total or partial change in contrast; q: electric charge; ITO: Sn-doped indium oxide; transparent conducting material used for electrochromic measures; PB, Prussian blue: [FeIIIFeII(CN)6]−, iron hexacyanoferrate; viologens: organic molecules based on 1,1-"disubstituted-4,4-bipyridinium salts"; ECP: electronic conducting polymer; MLCT; metal-ligand charge transfer; PEDOT: poly(3,4-ethylenedioxythiophene); LbL: Layer-by-Layer deposition; technique based on adsorption of alternate charged species; PANI: poly(aniline); HWCVD: hot wire chemical vapour deposition; LPEI/PB: polyethyleneimine/Prussian blue; PAH: poly(allylamine hydrochloride); PXV: poly(hexyl viologen); PDDA: poly(diallyldimethylammonium chloride).
1. Introduction
1.1. Electrochromism
In the last few years, the interest in solar energy has grown leading to the development of new technologies to convert and store energy from this inexhaustible source. The advantages of these technologies are evident but the most attractive feature is related to the reduction of environmental impact. Besides, a high amount of economic resources have been spent in this field due to the great interest in the car industry, aerospace and military applications, entertainment, etc.
A new class of optically active materials has been subject of great interest, especially those which show controlled absorption change. These materials are called chromogenics and they change their optical properties when exposed to different physical or chemical perturbations. When a reversible optical modification is observed as a consequence of the application of an electric voltage or current, the phenomenon is called electrochromism.1 In cases where more than two redox states are electrochemically available, the electrochromic material may exhibit several colors and can be described as poly-electrochromic. This principle has already been demonstrated in electrochromic car rearview mirrors, which automatically darken at night, when illuminated from behind by car headlights. These and many other applications make electrochromic materials highly sought after for commercial uses; the most widely known being mirrors, smart windows and displays.2
One characteristic group of electrochromic materials are those based on ion insertion, these materials being electronic and ionic conductors, where ions can be inserted into the compound matrix in order to compensate charge. This insertion must be fast and reversible, for example, in a reduction reaction, the gain of an electron needs to be accompanied by the insertion of an ion (I+) to keep the electroneutrality of the system:
where ECM represents the electrochromic material. The double insertion process leads to the change in the oxidation state of the material provoking modifications in its optical properties. The performance of an electrochromic system can be described by many parameters, but three of them are the most important, the electrochromic efficiency, the chromatic contrast and the response time.
The electrochromic efficiency (η) is related to the absorbance change (ΔA) when a certain amount of electric charge (q) is injected per unit area, and can be calculated by:
The electrochromic efficiency is expressed in cm2 C-1. For some classical electrochromic materials, like WO3, efficiencies of 115 cm2 C-1 are obtained, at 633 nm, and for TiO2, about 8 cm2 C-1 at 546 nm, have been reported.1
As η is a relative quantity, for practical purposes, it is important to analyse this value together with the chromatic contrast (ΔT %). This is an important point because it is possible to obtain high electrochromic efficiency in conditions where the contrast could be very low, which is a bad situation from a practical point of view, and that's why parameters, η and ΔT %, must always be analyzed together.3
Response time (τ) is the time required for an ECM to change from colored state to bleached one. For most devices, τ values are of the order of a few seconds, but in commercial, large area devices, like a window, response times of the order of some minutes are commonly found. Unfortunately, there is no consistency in the criteria employed for determining τ, it may be either the time necessary for changing the absorbance by an arbitrary amount, or the time needed to inject all or part of the charge.1,2
1.2. Electrochromic devices and materials
There are three major kinds of configurations for electrochromic devices: battery-like, solution-phase and hybrid structure, as shown in Figure 1. Optically transparent electrodes for delivering current are the substrates common to all configurations. These are nearly always Sn-doped indium oxide (ITO) or another doped form of tin oxide (TO). In the battery-like configuration, a thin film of electrochromic material coats both the working and counter electrodes, and an electrolyte separates them. The electrolyte may be either a polymer/gel or a thin solid film. Polymer/gel electrolytes lead to laminated sandwich structures while thin solid film electrolytes are the basis of all-thin film electrochromic coatings.
The solution-phase and hybrid electrochromic devices are also called self-erasing types, in which one or both of the color changing substances are dissolved in a liquid or gel electrolyte, where they can freely diffuse. These approaches have been used in commercially successful electrochromic mirrors, but they have also been applied to electrochromic windows. While battery-like electrochromic devices present extended open circuit memory, a continuous current is required to maintain the self-erasing device in the colored state, with the intensity of coloration being proportional to the current density.
An electrochromic device requires charge balance between the oppositely facing electrodes, in such a way that the charge inserted during the cathodic half-reaction must be exactly balanced by the charge extracted from the anodic side of the device.
The variety of compounds showing electrochromism can be divided into four groups: (i) transition metal systems; where those most described in literature are TiO2,4 crystalline WO35 and Prussian blue;6 (ii) organic systems; mainly 1,1-"disubstituted-4,4-bipyridinium salts", known as viologens.7 (iii) conducting polymers; among classical electronic conducting polymers (ECPs), the electrochromic properties of polypyrroles,8 polythiophenes and oligomers,9 and polyaniline10 are reported in the literature and (iv) metallopolymers; chromogenic properties typically arise from low-energy metal-to-ligant charge transfer (MLCT), intervalence charge transfer, intraligant excitation and related visible region electronic transitions.11
1.3. Electrochromic nanomaterials
Nanotechnology is an emerging field of science dedicated to increase control over material structures at nanoscale size in, at least, one dimension. Nanostructured materials have indeed become the focus of modern solid state physics, chemistry, solid state ionics, materials engineering, medical sciences and biotechnology.
In the case of nanoparticles, two fundamental factors distinguish them from bulk materials and both are related to the small dimension of the unitary particle. The size of the particle can determine electronic and physical properties of the material, called quantum size effects, which are experimentally observed as a shift towards higher energy values of the band edge, as compared to the typical value for the corresponding bulk material. Such effects were clearly demonstrated in a study of CdS nanocrystallites with different and well-defined size distributions.12 The other factor, and the most relevant for electrochromism, is centered at the high dispersity (large surface/volume ratio) associated with the particles. Physical and chemical properties of the semiconductor are particularly sensitive to the surface structure. To ensure short response times in electrochromics, fast charge compensation during the redox process is required; so that, when the material is immobilized as nanoparticles a high percentage of active material is at the surface and in direct contact with the electrolyte. This fact must drastically reduce the time response of the electrode leading to high performing devices.
Literature concerning the synthesis of inorganic nanoparticles is very broadly scoped and the preparation of nanoparticles of molybdenum oxide,13 nickel hydroxide14 and nickel oxide,15 cobalt hydroxide,16 Prussian blue,17 iridium oxide18 and tungsten oxide19 were reported. Nevertheless, few examples of the use of these nanoparticles in electrochromic applications can be found. The most widely used compound for electrochromic devices is titanium oxide as substrate for organic dyes, for the following reasons: the application of nanocrystalline TiO2 films for efficient dye-sensitized photovoltaic cells (Grätzel cells) has boosted the interest for these remarkable assemblies. The relevant properties of nanocrystalline films for electrochromic applications are their transparency to visible light, electronic conductivity, large surface area and affinity towards specific ligands. The derivatization of nanocrystalline films with different types of molecular monolayers led to, in addition to solar cells and electrochromic devices, to elaborate sensors,20 photoelectrocatalytic,21 electroluminescent22 and photoelectrochromic devices.23
The common principle of efficiency in these devices lies on fast interfacial electron transfer between the nanocrystalline material and the adsorbed modifier as well as on the high surface area of the substrate that amplifies optical phenomena by two or three orders of magnitude. The general principle of the electrochromism of a molecular monolayer adsorbed on TiO2 is depicted in Figure 2, electrons are injected from the conducting substrate into the conduction band of the semiconductor and from there, reduce the adsorbed organic chromophore. Provided the redox potential of that molecule, that lies above the conduction band edge, the process is reversible by application of a positive potential to the conductive substrate. In such a situation, the semi-conductor behaves, in fact, like a conductor for the adsorbed electroactive species. If, on the contrary, the redox potential is situated below the conduction band edge, the reduction process is irreversible.
Several electrochromic molecules were investigated as derivatizing agents. They all are composed of an electrochromophore (viologen) and an anchoring group (phosphate, carboxylate, salicilate, etc.). Nanoparticulated TiO2 films where also reported as being superficially modified by molecules of transition metal complexes presenting high electrochromic efficiency.24 Campus and Bonhote25 have shown the electrochromism of a system consisting in a nanocrystalline TiO2 films, as seen in Figure 3 (A), derivatized with five different viologens, which are shown in Figure 3 (B). These electrodes displayed different absorption features, with high contrast visible changes.
Bipyridine salts and viologens are widely employed as electrochromic electrodes due to their intense coloration when reduced. The color depends on the chemical nature of the substituents bonded to the nitrogen atom. On the other hand, it is also known that the reduction potential of the viologen can be tuned by changing the substituent, as it can be seen in Figure 3 (C). Alkyl substituents lead to blue-violet coloration; while, if the substituent is a cyano phenyl group (- C6H5CN) the coloration is shifted to green.26
Recently, the spectroelectrochemical properties of nanoporous electrodes prepared by spin coated colloidal SnO2:Sb have been investigated.27 Injection of electrons via the back contact results in a reversible color change of the material. At positive potentials the SnO2:Sb layer is bleached, whereas at negative potentials the electrode turns blue. This electrode exhibits very short response time (τ< 10 ms). Extended cycling between colored and bleached states (106 cycles) does not deteriorate the electrochromic material.
All the examples given above refer to the modification of one of the electrodes of an electrochromic device. However, as it was already explained, charge must be balanced between both, working and counter electrode. In this way, modifying both electrodes must attain a highly efficient electrochromic device. Cummings et al.28 proposed a device where both electrodes were superficially modified by nanoparticulated films containing an adsorved organic chromophore. A scheme of this device is shown in Figure 4, where the working electrode was assembled by TiO2 nanoparticles with attached bis(2-phosphonoethyl)-4,4'-bipyridinium and the counter electrode was composed by SnO2:Sb nanoparticles modified by phenothiazine.
Figure 5 shows the absorption spectra in the colored and bleached states at different three points of the electrochromic window (points A, B, and C depicted in Figure 5). It can be seen that under the reported conditions, the viologen modified nanostructured TiO2 electrode turns blue (position A), while the phenothiazine-modified nanostructured SnO2:Sb electrode turns red (position B). In a consistent way, the region where these electrodes overlap (position C) the electrochromic window turns blue-red.
The coloration rate of a 2.5×2.5 cm electrochromic window was measured following the application of a voltage of 1.2 V which biased the viologen modified nanostructured TiO2 film negative to the phenothiazine modified SnO2:Sb film. The coloration time, in this work, was defined as the time taken for the transmittance to decrease by two thirds of the difference between the steady state transmittances in both, the bleached and colored states; this parameter was reported to be about 250 ms. The bleaching rate of the same electrochromic window was measured by applying a voltage of 0.0 V to a previously colored device and it was about 105 ms. The coloration efficiency at 608 nm was about 270 cm2 C-1 and this window was relatively stable over 10,000 cycles under ambient laboratory conditions.
As cited before, WO3 is the most widely studied electrochromic material, due to the development of this material at nanoscale. Santato et al.19 described the synthesis and characterization of WO3 nanoparticles. Modified electrodes by using these nanoparticles produced electrochromic efficiencies of ca. 40 cm2 C-1, and high durability, being exposed to more than 10,000 cycles. Deepa et al.29 showed the formation of mesoporous WO3 electrodes (5-10 nm), presenting response times of 2-3 s and electrochromic efficiency of 90 cm2 C-1; similar results were obtained by Nishio et al.30 In order to obtain more conductive electrodes, consequently enhancing electrochromic properties, WO3 can be combined with other electrochromic materials, like hexacyanoferrates,31 or metallic nanoparticles can be inserted into WO3 matrix as shown by Park et al.,32 but surprisingly the electrode changed from cathodic coloration to anodic one. According to the authors this characteristic is related to forced ionic insertion due to the presence of metals, the response times reported for these electrodes were in the range of 3 to 5 s. Another study concerned the mixture of metallic nanoparticles and electrochromic materials, Ag and Au nanoparticles were incorporated on PEDOT conducting polymer, where higher absorbance was obtained.33
In a recent publication,34 WO3 nanorods and nanospheres were formed by hot wire chemical vapour deposition (HWCVD), and results are shown in Figure 6 (A). These nanostructures were immobilized onto substrates by electrophoresis leading to films with high porosity, as seen at Figure 6 (B). The electrochemical performance of different WO3 modified electrodes was tested in H2SO4 solution by cyclic voltammograms (CVs) for nanostructured, crystalline and amorphous WO3, the currents being normalized by the electrode surface and the mass of material deposited. Results are shown in Figure 7.
By comparing the cathodic charges of amorphous and crystalline tungsten oxide films with the nanoparticle modified electrode, it is clear that there is a higher charge-insertion density over the same period of time, indicating faster kinetics. According to authors, the cathodic charge spent for WO3 nanoparticles was about 32 mC cm2 mg1, compared with ca. 3 mC cm2 mg1 and 9 mC cm2 mg1 for crystalline and amorphous films, respectively. The cycling stability of WO3 nanoparticles modified electrode was examined in 1 mol L-1 H2SO4 (Figure 7B). It can be seen that the current response increases slightly during the course of 3,000 cycles, without a significant change in the shape or charge of the voltammograms, indicating excellent cycling stability of the nanoparticles. To verify this characteristic, the cycling stability of an amorphous WO3 film in the same electrolyte was also examined (Figure 7C). As it can be seen, the amorphous WO3 film degrades significantly after only 500 cycles.
1.4. Layer-by-layer deposition
Most electroactive polymers are deposited onto substrates by spin coating, dip coating, electropolymerization, or surface polymerization by chemical ways. An alternative and innovative approach for film formation is the layer-by-layer (LbL) assembly technique. In the classical LbL method, a charged substrate is exposed alternately to dilute aqueous solutions of polycations and polyanions, enabling the deposition of a polyelectrolyte complex as a thin film with controlled thickness and composition.35 The LbL technique results in smooth films that can include materials of any functionality such as light-emitting polymers,36 inorganic nanoparticles37 and biomolecules.38
In a recent publication, DeLongchamps and Hammond39 presented a "dual electrochromic" composite in which both polycation and polyanion species are cathodically coloring electrochromic species. The polycationic species, poly(hexyl viologen) (PXV) is colored in the reduced state due to the formation of a charge-transfer complex; while as polyanionic species, PEDOT was used. Both electrochromic compounds switch from transparent oxidized state to dark blue reduced one.
The composite switches from a transparent sky-blue color when oxidized, to a deeply absorptive purple/blue color when reduced. By increasing the composite thickness, a slightly darker color in the bleached state and a far more saturated color state are displayed. The gray scale of this composite is demonstrated at 0.4 V, where most of the PEDOT is reduced, but PXV remains oxidized. The chromatic contrast obtained with this window was 82.1% at 525 nm, much higher than the respective polymers; but coloration times are rather high, of ca. 1-4 s.
The LbL process can be extended to immobilize nanoparticles. Lvov and co-workers38 have shown the adsorption of SiO2 nanoparticles using PDDA as polycation. This approach opens the possibility of immobilizing different kinds of compounds synthetized as nanoparticles. Quartz crystal microbalance was used as a very efficient tool for following the immobilization process of each bilayer and a transversal view of the film can be obtained by scanning electron microscopy (SEM) showing the interconnectivity of the particles within the PDDA film.
For electrochromic electrodes, LbL technique was employed to immobilize Prussian blue nanoparticles39 by using LPEI as polycation, and the influence of the number of bilayers on the electrochromic behavior was analysed. Figure 8 shows the spectroelectrochemical experiments for 50 bilayers, where UV-Vis spectra were taken at different potentials, fully oxidized PB (deep blue) was achieved at 0.3 V, depicted by a well defined charge transfer band with an absorbance peak at 700 nm (Figure 8A). The switching speed was determined by dynamic changes in absorbance (at 700 nm) by applying a potential square wave program (−0.2 V for bleached and +0.6 V for colored states), Figure 8B. The results can be summarized in Table 1.
Recently, Baioni et al.40 reported the synthesis of copper hexacyanoferrate nanoparticles, a Prussian blue derivative, by employing ultrasound radiation. Prussian blue analogues are of great interest, because it is well known that PB lack electroactivity in Na+ media. These analogues act by substitution of one Fe atom by copper or nickel and preserve some of PB's properties, especially electrocatalysis of H2O2 reduction. Copper hexacyanoferrate nanoparticles were immobilized onto transparent electrodes by LbL technique, and color changes from light orange (reduced state) to brown (oxidized state) were followed. In Figure 9 the voltammograms for different number of bilayers recorded simultaneously with the change in absorbance at 540 nm are shown.
The immobilization of nanoparticles by the LbL technique is a very efficient strategy for the building up of different architectures, such as alternated Ni(OH)2 and Co(OH)2 nanostructured films. Hydroxide nanoparticles were synthesized by sonochemistry41 and the electrodes were prepared by using PAH as polycation and alternatively, colloidal suspensions of Ni(OH)2 or Co(OH)2 nanoparticles, as polyanions. Figure 10 shows the voltammograms obtained simultaneously with the T % vs. E profiles. Two different redox processes can be clearly distinguished, one corresponding to the Co(II)/Co(III) redox couple at less positive potentials and the other corresponding to the Ni(II)/Ni(III) couple at more positive potentials. This fact demonstrates the coexistance of the two chemical species and the connectivity among the different bilayers of nanoparticles.
The combination of organic chromophores and inorganic molecules is not restricted to TiO2 already described systems. Electrochromic properties of polyaniline and Prussian blue can be combined in a synergic way and were already described for electrodeposited films. The LbL assembly of Prussian Blue can be achieved by using poly(ethyleneimine, LPEI)39 or PAH17 and the successful combination of Prussian blue nanoparticles with polyaniline was recently reported.42 The individual contributions of PANI are related to broad reduction and oxidation peaks, with sloping shoulders, while PB contribution is observed as sharp and well defined peaks. These features illustrate that both materials are electrochemically active within the LbL assembled film, exhibiting explicit electrochemical signatures.
The spectroelectrochemistry of the PANI/PB nanocomposite reveals complete conversion from a pale yellow, transparent state to a high colored blue state with an absorbance band centered at approximately 750 nm. The broad absorbance band corresponding to the oxidized state increases linearly with film thickness. At 0.2 V, the spectrum exhibits absorbance at 400-450 nm and a broad absorbance band at 600-800 nm; the combination should result in a green hue. Response times of both, coloration and bleaching processes of LbL PANI/PB electrodes at different oxidation states and different amounts of bilayers have been reported being of the order of hundred of milliseconds till 30 bilayers deposition.42
The layer-by-layer technique allows the easy combination of different materials and a direct result of this approach is that it could provide multiple colored electrochromic films to support full-color displays or cheap and flexible color-adaptive raiment. The LbL technique was also reported for inorganic complexes,43 increasing in this way the possible applications in electrochromic devices.
2. Final Remarks
The combination of nanoparticles, chomophore organic molecules, transition metal complexes and conducting polymers together with the simplicity of the LbL method for preparing electrodes with defined architectures controlled at nanoscale level, seem to be the novel direction in electrochromics. Since the discovery of electrochromism, many efforts were made in order to obtain new architectures of modified electrodes; at this point, a great advance was achieved by the incorporation of nano TiO2-chromophore modified electrodes, presenting high electrochromic efficiencies and low response times. Additionally, the possibility of modification of counter-electrodes is a very interesting feature, once a wide variety of colors can be obtained by changing the potential.
Currently, the development of new techniques for tailoring electrodes seems to be the new direction in electrochromics. The LbL deposition is a low cost and easily handled technique where nanoparticles, organic molecules and polymers can be alternately deposited. Depending on their electrochromic behavior, many colorations can be achieved, without counter-electrode modification, by this means cheaper devices are found. The number of publications in this field is increasing sharply indicating that patents and commercial applications in large scale are becoming real in the not so far future.
Acknowledgements
The authors thank Brazilian agencies FAPESP (Proc. 03/10015-3), CNPq and Instituto do Milênio de Materiais Complexos for financial support. M. Vidotti would like to thank FAPESP and CNPq for scholarships granted (Proc. 03/00629-4 and 152312/2007-2, respectively).
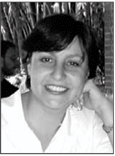
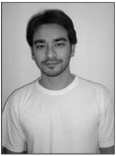
Marcio Vidotti received his BSc in Chemistry in 2002 and PhD in Physical Chemistry in 2007 from the Institute of Chemistry, Universidade de São Paulo, Brazil, under the supervision of Prof. S.I. Cordoba de Torresi working with nanoparticles applied to electrochromic devices. Currently, he is a pos-doc fellow at the Institute of Chemistry, University of Campinas, Brazil under the supervision of Prof. Lauro Kubota. His interests are focused in nanotechnology and nanomaterials applied to electrochemical devices.
References
1. Somani, P. R., Radhakrishnan, S.; Mater. Chem. Phys. 2003, 77, 117; Monk P. M. S.; Mortimer R. J.; Rosseinsky D. R.; Electrochromism: Fundamentals and Applications; John Wiley & Sons: New York, 1995; Rowley N. M.; Mortimer R. J.; Sci. Prog. 2002, 85, 243; Mortimer, R. J.; Chem. Soc. Rev. 1997, 26, 147; De Oliveira, S. C.; Torresi, R. M.; Córdoba de Torresi, S. I.; Quim. Nova 2000, 23, 79; Livage J; Ganguli D.; Sol. Energy Mater. 2001, 68, 365.
2. Rauh, R. D.; Electrochim. Acta 1999, 44, 3165; Rosseinsky D. R.; Mortimer R. J.; Adv. Mater. 2001, 13, 783; Monk, P.M.S.; Mortimer, R.J.; Rosseinky, D. R.; Electrochromism and Electrochromic Devices, University Press: Cambridge, 2007.
3. Cordoba de Torresi, S. I.; Gorenstein, A.; Electrochim. Acta 1992, 37, 2015.
4. Cantao, M. P.; Cisneros, J. I.; Torresi, R. M.; Thin Solid Films 1995, 259, 70; Cantao, M. P.; Cisneros, J. I.; Torresi, R. M.; J. Phys. Chem. 1994, 98, 4865; Harizanov, O.; Harizanova, A.; Sol. Energy Mater. 2000, 63, 185.
5. Granqvist, C. G.; Electrochim. Acta 1999, 44, 3005; Yu, Z.; Jia, X.; Du, J.; Zhang, J.; Sol. Energy Mater. 2000, 64, 55; Gabrielli, C.; Keddam, M.; Perrot, H.; Torresi, R.; J. Electroanal. Chem. 1994, 378, 85; Cordoba de Torresi, S. I.; Gorenstein, A.; Torresi, R. M.; Vazquez, M. V.; J. Electroanal. Chem. 1991, 318, 131.
6. Ellis, D.; Eckhoff, M.; Neff, V. D.; J. Phys. Chem. 1981, 85, 1225; DeLongchamp, D. M.; Kastantin, M.; Hammond, P. T.; Chem. Mater. 2003, 15, 1575.
7. Argun, A. A.; Aubert, P.-H.; Thompson, B. C.; Schwendeman, I.; Gaupp, C. L.; Hwang, J.; Pinto, N. J.; Tanner, D. B.; MacDiarmid, A. G.; Reynolds, J. R.; Chem. Mater. 2004, 16, 4401; Mortimer, R. J.; Electrochim. Acta 1999, 44, 2971.
8. Córdoba de Torresi, S. I.; Torresi, R. M.; Ciampi, G.; Luengo, C. A.; J. Electroanal. Chem. 1994, 377, 283; Rocco, A. M.; De Paoli, M.-A.; Zanelli, A.; Mastragostino, M.; Electrochim. Acta 1996, 41, 2805.
9. Guerrero, D. J.; Ren, X.; Ferraris, J. P.; Chem. Mater. 1994, 6, 1437.
10. Diaz, A. F.; Logan, J. A.; J. Electroanal. Chem. 1980, 111, 111; Bernard, M. C.; Cordoba de Torresi S.I.; Hugot-Le Goff, A.; Sol. Energy Mater. 1992, 25, 225; Bernard, M. C.; Bich, V. T.; Cordoba de Torresi, S.I.; Hugot-Le Goff, A.; Synth. Met. 1997, 84, 785; Gazotti, W. A.; Jannini, M. J. D.; Cordoba de Torresi, S. I.; De Paoli, M.-A.; J. Electroanal. Chem. 1997, 440, 193.
11. Beer, P. D.; Kocian, O.; Mortimer, R. J.; Ridgway, C.; J. Chem. Soc. Faraday Trans. 1993, 89, 333.
12. Alivisatos, A. P.; J. Phys. Chem. 1996, 100, 13226; Trindade, T.; O'Brien, P.; Pickett, N. L.; Chem. Mater. 2001, 13, 3843; Wang Y.; Herron, N.; J. Phys. Chem. 1991, 95, 525.
13. Pol, S. V.; Pol, V. G.; Kessler, V. G.; Seisenbaeva, G. A.; Sung, M.; Asai, S.; Gedanken, A.; J. Phys. Chem. B 2004, 108, 6322.
14. Jeevanandam, P.; Koltypin, Y.; Gedanken, A.; Nano Lett. 2001, 1, 263.
15. Carnes, C. L.; Stipp, J.; Klabunde, K. J.; Bonevich, J.; Langmuir 2002, 18, 1352.
16. Jeevanandam, P.; Koltypin, Y.; Gedanken, A.; Mastai, Y.; J. Mater. Chem. 2000, 10, 511.
17. Fiorito, P. A.; Gonçales, V. R.; Ponzio, E. A.; Cordoba de Torresi, S. I.; Chem. Commun. 2005, 366.
18. Pauporte, T.; Andolfatto, F.; Durand, R.; Electrochim. Acta 1999, 45, 431.
19. Santato, C.; Odziemkowski, M.; Ulmann, M.; Augustynski, J.; J. Am. Chem. Soc. 2001, 123, 10639.
20. Cosnier, S.; Gondran, C.; Senillou, A.; Graetzel, M.; Vlachopoulos, N.; Electroanalysis 1997, 9, 1387.
21. Mayor, M.; Hagfeldt, A.; Graetzel, M.; Walder, L.; Chimia 1996, 50, 47.
22. Athanassov, Y.; Rotzinger, F. P.; Pechy, P.; Graetzel, M.; J. Phys. Chem. B 1997, 101, 2558.
23. Bonhote, P.; Moser, J.-E.; Humphry-Baker, R.; Vlachopoulos, N.; Zakeeruddin, S. M.; Walder, L.; Graetzel, M.; J. Am. Chem. Soc. 1999, 121, 1324.
24. Nogueira, A. F.; Toma, S. H.; Vidotti, M.; Formiga, A. L. B.; Cordoba de Torresi, S. I.; Toma, H. E.; New J. Chem. 2005, 29, 320.
25. Campus, F.; Bonhote, P.; Gratzel, M.; Heinen, S.; Walder, L.; Sol. Energy Mater. 1999, 56, 281; Bonhote, P.; Gogniat, E.; Campus, F.; Walder, L.; Gratzel, M.; Displays 1999, 20, 137.
26. Imabayashi, S.; Kitamura, N.; Tazuke, S.; Tokuda, K.; J. Electroanal. Chem. 1988, 239, 397; Rosseinsky D. R.; Monk, P. M. S.; Sol. Energy Mater. 1992, 25, 201.
27. zum Felde, U.; Haase, M.; Weller, H.; J. Phys. Chem. B 2000, 104, 9388.
28. Cummins, D.; Boschloo, G.; Ryan, M.; Corr, D.; Rao, S. N.; Fitzmaurice, D.; J. Phys. Chem. B 2000, 104, 11449.
29. Deepa, M.; Srivastava, A K.; Sood, K. N.; Agnihotry S. A.; Nanotechnology 2006, 17, 2625.
30. Nishio, K.; Iwata, K.; Masuda, H.; Electrochem. Solid-State Lett. 2003, 6, H21.
31. Hong, S. F.; Chen, L. C.; Electrochim. Acta 2008, 53, 5306.
32. Park, K. W.; Electrochim. Acta 2005, 50, 4690; Park, K. W.; Song, Y. J.; Lee, J. M.; Han, S. B.; Electrochem. Commun. 2007, 9, 2111; Park, K. W.; Shin, H. S.; Seong, T. Y.; Sung. E. Y.; Appl. Phys. Lett. 2006, 88, 211107.
33. Namboothiry, M. G.A.; Zimmerman, T.; Coldren, F. M.; Liu, L.; Kim, K.; Carroll, D. L.; Synth. Metals 2007, 157, 580.
34. Lee, S. H.; Deshpande, R.; Parilla, P. A.; Jones, K. M.; To, B.; Mahan, A. H.; Adv. Mater. 2006, 18, 763.
35. Decher, G.; Science 1997, 277, 1232.
36. Fou, A. C.; Onitsuka, O.; Ferreira, M.; Rubner, M. F.; Hsieh, B. R.; J. Appl. Phys. 1996, 79, 7501.
37. Lvov, Y.; Ariga, K.; Onda, M.; Ichinose, I.; Kunitake, T.; Langmuir 1997, 13, 6195; Lvov, Y. M.; Rusling, J. F.; Thomsen, D. L.; Papadimitrakopoulos, F.; Kawakami, T.; Kunitake, T.; Chem. Commun. 1998, 1229.
38. Decher, G.; Hong, J. D.; Lowack, K.; Lvov, Y.; Schmitt, J.; NATO Adv. Sci. Inst. Ser. C Math. Phys. Sci. 1994, 446, 267.
39. DeLongchamp, D. M.; Hammond, P. T.; Adv. Funct. Mater. 2004, 14, 224.
40. Baioni, A. P.; Vidotti, M.; Fiorito, P. A.; Ponzio, E. A.; Córdoba de Torresi. S. I.; Langmuir 2007, 27, 6796.
41. Vidotti, M.; Greco, C. V.; Ponzio, E. A.; Córdoba de Torresi, S. I.; Electrochem. Comm. 2006, 8, 554; Vidotti, M.; Salvador, R. P.; Ponzio, E. A.; Córdoba de Torresi. S. I.; J. Nanosci. Nanotechnol. 2007, 7, 3221; Vidotti, M.; Silva, M. R.; Salvador, R. P.; Córdoba de Torresi, S. I.; Dall'Antonia, L. H.; Electrochim. Acta 2008, 53, 4030.
42. DeLongchamp, D. M.; Hammond, P. T.; Chem. Mater. 2004, 16, 4799.
43. Shinbo, K.; Onishi, K.; Miyabayashi, S.; Takahashi, K.; Katagiri, S.; Kato, K.; Kaneko, F.; Advincula, R. C.; Thin Solid Films 2003, 438-439, 177.
Received: March 31, 2008
Web Release Date: August 22, 2008
FAPESP helped in meeting the publication costs of this article.
-
1Somani, P. R., Radhakrishnan, S.; Mater. Chem. Phys. 2003, 77, 117;
- Monk P. M. S.; Mortimer R. J.; Rosseinsky D. R.; Electrochromism: Fundamentals and Applications; John Wiley & Sons: New York, 1995;
- Rowley N. M.; Mortimer R. J.; Sci. Prog. 2002, 85, 243;
- Mortimer, R. J.; Chem. Soc. Rev. 1997, 26, 147;
- De Oliveira, S. C.; Torresi, R. M.; Córdoba de Torresi, S. I.; Quim. Nova 2000, 23, 79;
- Livage J; Ganguli D.; Sol. Energy Mater 2001, 68, 365.
- 2. Rauh, R. D.; Electrochim. Acta 1999, 44, 3165;
- Rosseinsky D. R.; Mortimer R. J.; Adv. Mater 2001, 13, 783;
- Monk, P.M.S.; Mortimer, R.J.; Rosseinky, D. R.; Electrochromism and Electrochromic Devices, University Press: Cambridge, 2007.
- 3. Cordoba de Torresi, S. I.; Gorenstein, A.; Electrochim. Acta 1992, 37, 2015.
- 4. Cantao, M. P.; Cisneros, J. I.; Torresi, R. M.; Thin Solid Films 1995, 259, 70;
- Cantao, M. P.; Cisneros, J. I.; Torresi, R. M.; J. Phys. Chem. 1994, 98, 4865;
- Harizanov, O.; Harizanova, A.; Sol. Energy Mater. 2000, 63, 185.
- 5. Granqvist, C. G.; Electrochim. Acta 1999, 44, 3005;
- Yu, Z.; Jia, X.; Du, J.; Zhang, J.; Sol. Energy Mater. 2000, 64, 55;
- Gabrielli, C.; Keddam, M.; Perrot, H.; Torresi, R.; J. Electroanal. Chem. 1994, 378, 85;
- Cordoba de Torresi, S. I.; Gorenstein, A.; Torresi, R. M.; Vazquez, M. V.; J. Electroanal. Chem. 1991, 318, 131.
- 6. Ellis, D.; Eckhoff, M.; Neff, V. D.; J. Phys. Chem. 1981, 85, 1225;
- DeLongchamp, D. M.; Kastantin, M.; Hammond, P. T.; Chem. Mater. 2003, 15, 1575.
- 7. Argun, A. A.; Aubert, P.-H.; Thompson, B. C.; Schwendeman, I.; Gaupp, C. L.; Hwang, J.; Pinto, N. J.; Tanner, D. B.; MacDiarmid, A. G.; Reynolds, J. R.; Chem. Mater. 2004, 16, 4401;
- Mortimer, R. J.; Electrochim. Acta 1999, 44, 2971.
- 8. Córdoba de Torresi, S. I.; Torresi, R. M.; Ciampi, G.; Luengo, C. A.; J. Electroanal. Chem. 1994, 377, 283;
- Rocco, A. M.; De Paoli, M.-A.; Zanelli, A.; Mastragostino, M.; Electrochim. Acta 1996, 41, 2805.
- 9. Guerrero, D. J.; Ren, X.; Ferraris, J. P.; Chem. Mater. 1994, 6, 1437.
- 10. Diaz, A. F.; Logan, J. A.; J. Electroanal. Chem. 1980, 111, 111;
- Bernard, M. C.; Cordoba de Torresi S.I.; Hugot-Le Goff, A.; Sol. Energy Mater. 1992, 25, 225;
- Bernard, M. C.; Bich, V. T.; Cordoba de Torresi, S.I.; Hugot-Le Goff, A.; Synth. Met. 1997, 84, 785;
- Gazotti, W. A.; Jannini, M. J. D.; Cordoba de Torresi, S. I.; De Paoli, M.-A.; J. Electroanal. Chem. 1997, 440, 193.
- 11. Beer, P. D.; Kocian, O.; Mortimer, R. J.; Ridgway, C.; J. Chem. Soc. Faraday Trans. 1993, 89, 333.
- 12. Alivisatos, A. P.; J. Phys. Chem. 1996, 100, 13226;
- Trindade, T.; O'Brien, P.; Pickett, N. L.; Chem. Mater. 2001, 13, 3843;
- Wang Y.; Herron, N.; J. Phys. Chem. 1991, 95, 525.
- 13. Pol, S. V.; Pol, V. G.; Kessler, V. G.; Seisenbaeva, G. A.; Sung, M.; Asai, S.; Gedanken, A.; J. Phys. Chem. B 2004, 108, 6322.
- 14. Jeevanandam, P.; Koltypin, Y.; Gedanken, A.; Nano Lett. 2001, 1, 263.
- 15. Carnes, C. L.; Stipp, J.; Klabunde, K. J.; Bonevich, J.; Langmuir 2002, 18, 1352.
- 16. Jeevanandam, P.; Koltypin, Y.; Gedanken, A.; Mastai, Y.; J. Mater. Chem. 2000, 10, 511.
- 17. Fiorito, P. A.; Gonçales, V. R.; Ponzio, E. A.; Cordoba de Torresi, S. I.; Chem. Commun 2005, 366.
- 18. Pauporte, T.; Andolfatto, F.; Durand, R.; Electrochim. Acta 1999, 45, 431.
- 19. Santato, C.; Odziemkowski, M.; Ulmann, M.; Augustynski, J.; J. Am. Chem. Soc. 2001, 123, 10639.
- 20. Cosnier, S.; Gondran, C.; Senillou, A.; Graetzel, M.; Vlachopoulos, N.; Electroanalysis 1997, 9, 1387.
- 21. Mayor, M.; Hagfeldt, A.; Graetzel, M.; Walder, L.; Chimia 1996, 50, 47.
- 22. Athanassov, Y.; Rotzinger, F. P.; Pechy, P.; Graetzel, M.; J. Phys. Chem. B 1997, 101, 2558.
- 23. Bonhote, P.; Moser, J.-E.; Humphry-Baker, R.; Vlachopoulos, N.; Zakeeruddin, S. M.; Walder, L.; Graetzel, M.; J. Am. Chem. Soc. 1999, 121, 1324.
- 24. Nogueira, A. F.; Toma, S. H.; Vidotti, M.; Formiga, A. L. B.; Cordoba de Torresi, S. I.; Toma, H. E.; New J. Chem. 2005, 29, 320.
- 25. Campus, F.; Bonhote, P.; Gratzel, M.; Heinen, S.; Walder, L.; Sol. Energy Mater. 1999, 56, 281;
- Bonhote, P.; Gogniat, E.; Campus, F.; Walder, L.; Gratzel, M.; Displays 1999, 20, 137.
- 26. Imabayashi, S.; Kitamura, N.; Tazuke, S.; Tokuda, K.; J. Electroanal. Chem. 1988, 239, 397;
- Rosseinsky D. R.; Monk, P. M. S.; Sol. Energy Mater. 1992, 25, 201.
- 27. zum Felde, U.; Haase, M.; Weller, H.; J. Phys. Chem. B 2000, 104, 9388.
- 28. Cummins, D.; Boschloo, G.; Ryan, M.; Corr, D.; Rao, S. N.; Fitzmaurice, D.; J. Phys. Chem. B 2000, 104, 11449.
- 29. Deepa, M.; Srivastava, A K.; Sood, K. N.; Agnihotry S. A.; Nanotechnology 2006, 17, 2625.
- 30. Nishio, K.; Iwata, K.; Masuda, H.; Electrochem. Solid-State Lett. 2003, 6, H21.
- 31. Hong, S. F.; Chen, L. C.; Electrochim. Acta 2008, 53, 5306.
- 32. Park, K. W.; Electrochim. Acta 2005, 50, 4690;
- Park, K. W.; Song, Y. J.; Lee, J. M.; Han, S. B.; Electrochem. Commun 2007, 9, 2111;
- Park, K. W.; Shin, H. S.; Seong, T. Y.; Sung. E. Y.; Appl. Phys. Lett 2006, 88, 211107.
- 33. Namboothiry, M. G.A.; Zimmerman, T.; Coldren, F. M.; Liu, L.; Kim, K.; Carroll, D. L.; Synth. Metals 2007, 157, 580.
- 34. Lee, S. H.; Deshpande, R.; Parilla, P. A.; Jones, K. M.; To, B.; Mahan, A. H.; Adv. Mater. 2006, 18, 763.
- 35. Decher, G.; Science 1997, 277, 1232.
- 36. Fou, A. C.; Onitsuka, O.; Ferreira, M.; Rubner, M. F.; Hsieh, B. R.; J. Appl. Phys. 1996, 79, 7501.
- 37. Lvov, Y.; Ariga, K.; Onda, M.; Ichinose, I.; Kunitake, T.; Langmuir 1997, 13, 6195;
- Lvov, Y. M.; Rusling, J. F.; Thomsen, D. L.; Papadimitrakopoulos, F.; Kawakami, T.; Kunitake, T.; Chem. Commun. 1998, 1229.
- 38. Decher, G.; Hong, J. D.; Lowack, K.; Lvov, Y.; Schmitt, J.; NATO Adv. Sci. Inst. Ser. C Math. Phys. Sci. 1994, 446, 267.
- 39. DeLongchamp, D. M.; Hammond, P. T.; Adv. Funct. Mater. 2004, 14, 224.
- 40. Baioni, A. P.; Vidotti, M.; Fiorito, P. A.; Ponzio, E. A.; Córdoba de Torresi. S. I.; Langmuir 2007, 27, 6796.
- 41. Vidotti, M.; Greco, C. V.; Ponzio, E. A.; Córdoba de Torresi, S. I.; Electrochem. Comm. 2006, 8, 554;
- Vidotti, M.; Salvador, R. P.; Ponzio, E. A.; Córdoba de Torresi. S. I.; J. Nanosci. Nanotechnol. 2007, 7, 3221;
- Vidotti, M.; Silva, M. R.; Salvador, R. P.; Córdoba de Torresi, S. I.; Dall'Antonia, L. H.; Electrochim. Acta 2008, 53, 4030.
- 42. DeLongchamp, D. M.; Hammond, P. T.; Chem. Mater. 2004, 16, 4799.
- 43. Shinbo, K.; Onishi, K.; Miyabayashi, S.; Takahashi, K.; Katagiri, S.; Kato, K.; Kaneko, F.; Advincula, R. C.; Thin Solid Films 2003, 438-439, 177.
Publication Dates
-
Publication in this collection
03 Oct 2008 -
Date of issue
2008
History
-
Received
31 Mar 2008 -
Accepted
22 Aug 2008